NESTKING'S SOFTWARE
5 MIN READ TIME
Feature showcase: NestKing's Magic Tool

NestKing’s Magic Tool revolutionizes composite fabrication by addressing common industry challenges such as inaccurate cuts, material waste, and time-consuming processes. It optimizes geometries, corrects imperfections, and connects facets seamlessly, providing precise and efficient design capabilities.
This innovative tool has been successfully implemented in industries like aerospace and automotive, significantly improving production times and material efficiency. By offering advanced features through an intuitive interface, NestKing’s Magic Tool helps manufacturers streamline workflows and enhance product quality.
In the high-stakes world of composite material fabrication, precision and efficiency are not merely desirable—they are critical. For many professionals in the industry, the process of designing composite cuts can be fraught with challenges. NestKing software, more specifically its Magic Tool feature, addresses these pain points head-on. We delve into how the Magic Tool can transform your workflow, making it an essential asset for manufacturers seeking to improve their processes.
Professionals in composite fabrication often face several key challenges:
- Inaccurate Cuts - Even slight inaccuracies can compromise the integrity of composite materials.
- Material Waste - Inefficient cutting leads to excessive waste, driving up costs and environmental impact.
- Time-Consuming Processes - Manual corrections and adjustments can significantly slow down production.
- Complex Geometry Management - Handling intricate geometries and ensuring they are correctly interpreted by cutting machines can be difficult.
- Optimization and Cleanup - Ensuring the initial geometry is clean and optimized for further processing.
How the NestKing’s Magic Tool Provides Solutions
“Inaccurate cuts can lead to subpar products and increased material costs.”
The Magic Tool’s advanced algorithms ensure that every cut is precise. Cleaning up the geometry and putting inner lines on the correct layer helps create the exact outer shape required. This accuracy reduces waste and enhances product quality.
Minimizing Material Waste
“Excessive material waste is both costly and environmentally damaging.”
The Magic Tool excels in connecting single facets from DXF files into one solid line, dealing effectively with zigzags and V-darts. This optimization ensures minimal material waste, translating to significant cost savings and a smaller environmental footprint.
Streamlined Processes
“Manual corrections are time-consuming and prone to errors.”
With features like batch processing and real-time adjustment, the Magic Tool allows users to mark entire patterns and apply corrections swiftly. The intuitive dialog box provides a range of settings (angle tolerance, geometric tolerance, snap distance) to fine-tune the process, saving valuable time.
Handling Complex Geometries
“Managing complex geometries and ensuring they are correctly interpreted by cutting machines can be challenging.”
The Magic Tool's ability to clean up and optimize geometries makes handling complex designs straightforward. It ensures that even the most intricate patterns are accurately prepared for cutting, eliminating the headaches associated with manual adjustments.
“Ensuring the initial geometry is clean and optimized for further processing.”
The Magic Tool helps clean up the geometry, putting inner lines on the correct layer and creating the desired outer shape. It effectively connects single facets from DXF files, converting them into one solid line and dealing with imperfections like zigzags and V-darts.
NestKing software, with its innovative Magic Tool feature, is revolutionizing the design of composite material cuts. By addressing common pain points such as inaccuracies, waste, and time-consuming processes, NestKing offers a powerful solution for manufacturers looking to enhance their workflows.
Ready to transform your composite fabrication process? Discover how NestKing’s Magic Tool can make a difference. Contact our team for a demonstration and see the impact for yourself.
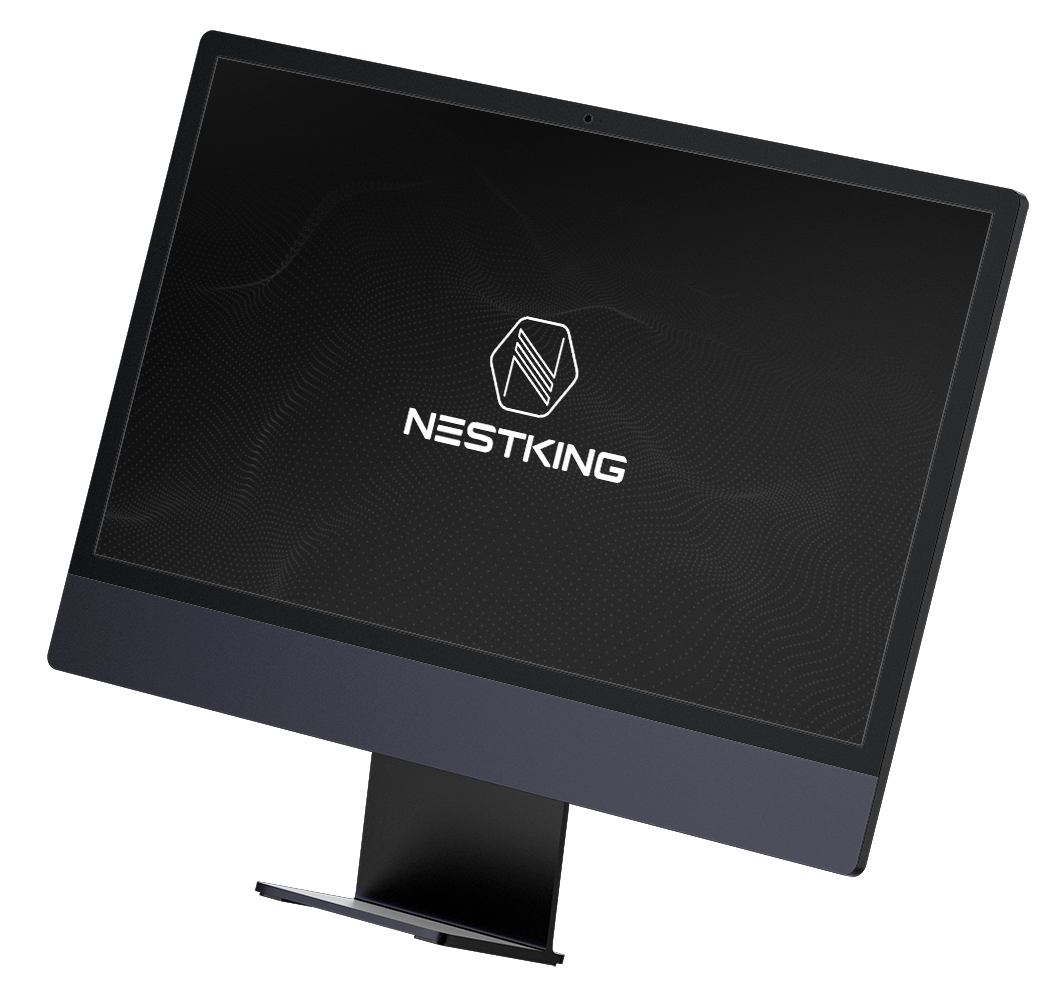
Get in touch
and we’ll get back to you as soon as possible.