PLYWIZ'S SOFTWARE
5 MIN READ TIME
Revolutionizing Composite Fabrication with PlyWiz's Advanced Solutions

In the world of composite material fabrication, efficiency and precision are paramount. PlyWiz's innovative software transforms complex and error-prone cutting processes into streamlined operations.
This blog explores how PlyWiz enhances the production of fiber composite cuts, making it indispensable in industries that rely on precision and efficiency.
Transforming Layup Creation Processes
PlyWiz simplifies the creation of complex layer structures in composite materials. Its capabilities extend to generating accurate plybooks and automating the offset in joints to enhance component strength. This level of automation significantly reduces the effort and potential for errors, ensuring that high-quality components are consistently produced.
Core Features of PlyWiz
- Plybook Creation - Automates the compilation of manufacturing orientations and sequences, crucial for meeting specific strength and quality requirements.
- Automated Offset Generation - Enhances joint integrity by automatically adjusting offsets, preventing weak spots in final products.
- Superior Nesting Capability - Minimizes material waste and optimizes machine time, translating into cost savings and environmental benefits.
- Automated Labeling - Each cutout is clearly labeled, simplifying the assembly process and reducing the chance of errors.
- Weight Determination - Calculates the weight of each cutout, crucial for applications where precise weight distribution is necessary.
Advantages Over Traditional Methods
The traditional methods of generating cuts for composite materials are not only time-consuming but also prone to inaccuracies that can compromise the integrity of the final product. PlyWiz's software streamlines this process, offering a faster, more intuitive experience compared to conventional 2D and 3D design tools. Here are some benefits highlighted:
- Reduced Design Times - Quick adjustments and real-time updates to designs make the development process more agile.
- Short Training Period - PlyWiz is designed to be user-friendly, requiring minimal training for new users.
- Fast and Efficient Implementation of Changes - Modifications to designs can be implemented quickly without the need to start over, saving valuable time and resources.
- High Flexibility - The software can be customized to suit specific customer needs, enhancing its applicability across various industries.
- Customer-Centric Innovations
- PlyWiz's commitment to customer satisfaction is evident in its flexible approach to software customization. This allows users to request modifications tailored to their specific production needs, ensuring that the software continues to provide value as industry demands evolve.
Industry Applications and Impact
PlyWiz's technology is versatile, supporting industries ranging from aerospace to automotive, where precision and efficiency are crucial. The software's ability to interface seamlessly with major CAD platforms like Catia, Solidworks, and Siemens NX, and its compatibility with any industry-standard cutter, underscores its broad applicability.
In conclusion...
PlyWiz is more than just a design tool; it is a comprehensive solution that addresses several critical aspects of composite component manufacturing. By reducing waste, optimizing workflows, and ensuring product integrity, PlyWiz not only supports sustainable manufacturing practices but also boosts profitability and efficiency. Industries looking to innovate and improve their composite cutting processes will find PlyWiz an invaluable ally.
For those interested in exploring PlyWiz's capabilities further, try out the demo or contact us so we can provide additional insights and personalized consultations.
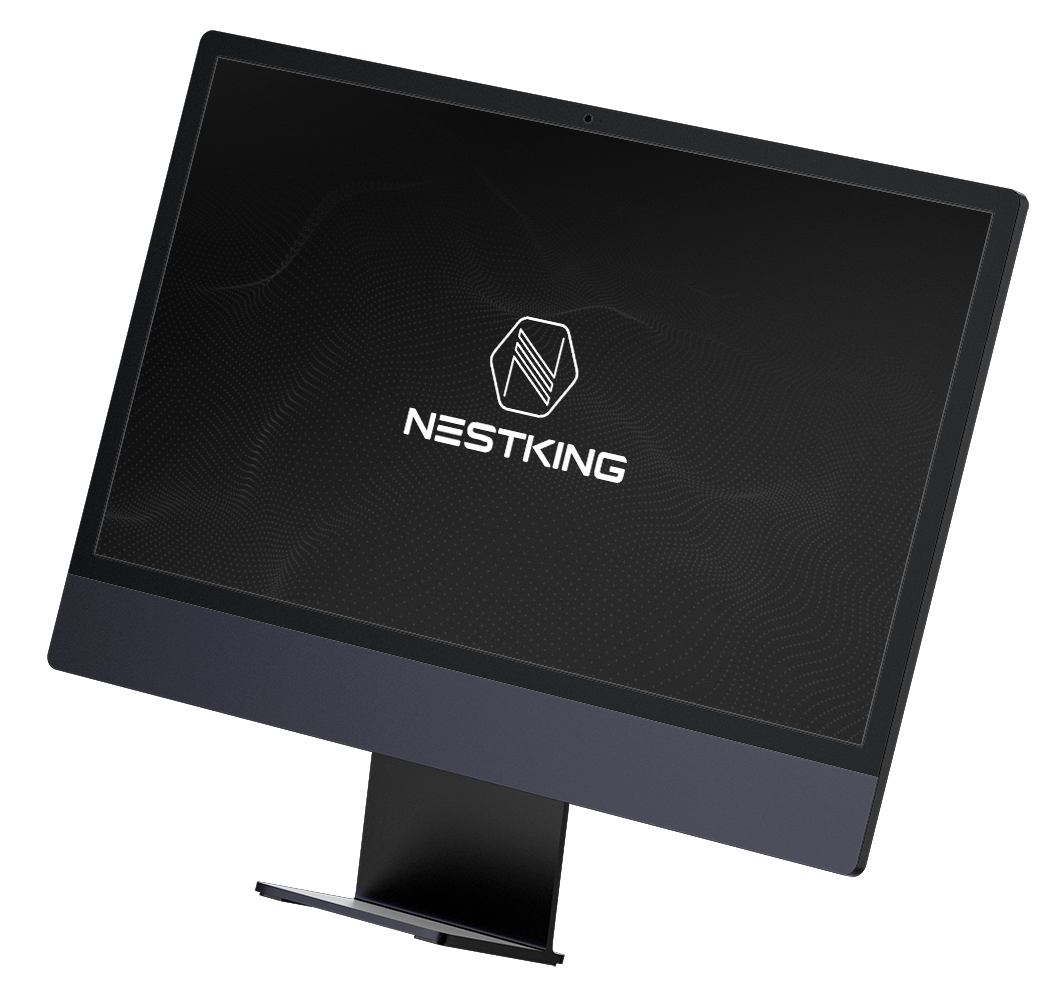
Get in touch
Fill out the form below with your details and message,
and we’ll get back to you as soon as possible.
and we’ll get back to you as soon as possible.